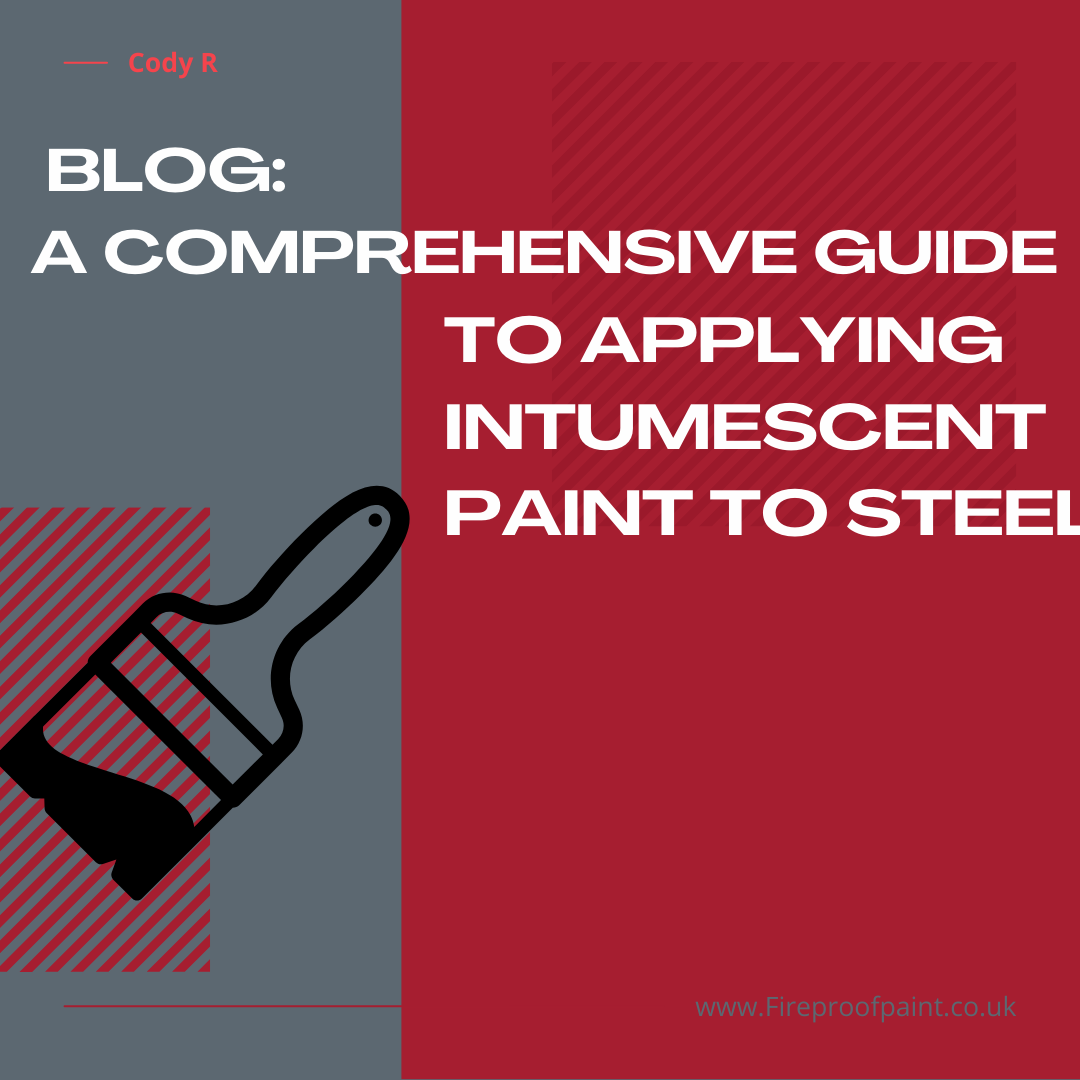
A Comprehensive Guide to Applying Intumescent Paint to Steel
Intumescent steel paint is one of our best sellers here at International Passive Fire.
Intumescent paint is an essential fire protection solution for steel structures. It expands when exposed to high temperatures, forming an insulating layer that protects the steel from critical heat levels. Applying intumescent paint correctly ensures optimal performance and longevity.
In this guide, we’ll cover the key steps involved in cleaning, priming, applying, and top-coating steel surfaces. We’ll also reference our leading brands that we supply such as Nullifire, Jotun, Sherwin-Williams, Thermoguard, and Envirograf to provide insight into trusted products in the industry.
Intumescent paints can also be found in different types (solvent-based, water-based, and epoxy intumescent paint). The primary differences between solvent-based, water-based, and epoxy intumescent paints lie in their composition, application, and performance characteristics. Here’s an overview:
Solvent-Based Intumescent Paints
Solvent-based intumescent paints use organic solvents as the carrier for intumescent chemicals, offering high durability and excellent adhesion to steel surfaces. They are resistant to moisture and environmental factors, making them suitable for both indoor and outdoor applications. While they dry faster than water-based paints, they are slower to cure compared to epoxy options. These paints perform well in variable weather conditions and have a long shelf life, but their high VOC content poses environmental and health concerns, necessitating proper ventilation during application and specialized handling for disposal. Typically applied using spray equipment, they require attention to safety and regulatory compliance.
Water-Based Intumescent Paints
Water-based intumescent paints use water as the solvent, making them an environmentally friendly option with low VOC emissions and minimal odor compared to solvent-based alternatives. These paints are ideal for interior environments and can be applied using brushes, rollers, or sprayers. However, they require controlled conditions, such as stable temperature and humidity, for proper drying and curing, which is typically slower than that of solvent-based paints. Their advantages include easy cleanup with water and safe application in occupied spaces. On the downside, they are more sensitive to humidity and weather during application and less durable in extreme conditions unless protected with a topcoat.
Epoxy Intumescent Paints
Epoxy intumescent paints are a two-component system comprising a resin and a hardener, designed for exceptional durability and resistance to mechanical damage, moisture, and harsh chemicals. Commonly used in high-performance environments such as offshore structures and petrochemical facilities, they are capable of withstanding extreme environmental conditions without degrading. Application requires skilled professionals and precise mixing ratios to ensure proper curing, with spraying being the most typical method. These paints offer superior long-term performance, weather resistance, excellent adhesion, and impact resistance, making them ideal for harsh environments like marine and industrial settings. However, they are more expensive than water- or solvent-based alternatives and involve a more complex application process with strict curing requirements.
Comparison Summary
Feature | Solvent-Based | Water-Based | Epoxy |
---|---|---|---|
Drying Time | Moderate | Slow | Fast |
VOC Emissions | High | Low | Low |
Durability | High | Moderate | Very High |
Environmental Use | Indoor/Outdoor | Mostly Indoor | Harsh Environments |
Cost | Moderate | Low | High |
Ease of Application | Moderate | Easy | Complex |
Choosing the Right Type
We can help you pick the right paint for your job but the best type of intumescent paint depends on the specific project requirements:
- Water-based: Suitable for interiors and projects requiring low VOC emissions.
- Solvent-based: Ideal for general outdoor applications with moderate environmental exposure.
- Epoxy: Perfect for industrial or offshore applications requiring extreme durability and environmental resistance.
If you are looking for certification of Intumescent paint you must contact us via the link , email ([email protected]) or call (01752 690997) to discuss your specification.
Step – Step Guide on Application
Step 1: Surface Preparation – Cleaning the Steel
Proper surface preparation is the cornerstone of a successful intumescent paint application. Steel surfaces must be free from rust, grease, dust, and other contaminants.
- Cleaning: Use industrial-grade degreasers or solvent-based cleaners to remove oil and grease. For stubborn dirt, abrasive blasting (to a minimum SA2.5 standard) is often recommended.
- Rust Removal: Any rust must be removed to avoid adhesion issues. Techniques like mechanical grinding or chemical rust removers may be required depending on the severity of corrosion.
- Inspection: Once cleaned, inspect the steel for any imperfections or residues. A smooth, clean surface enhances adhesion and ensures uniform application of subsequent layers.
Step 2: Priming the Steel Surface
Priming is a critical step as it provides a protective barrier against corrosion and promotes the adhesion of the intumescent coating.
We recommend a primer for all jobs requiring paint.
- Choose the Right Primer: Most manufacturers, like Sherwin-Williams and Jotun, offer primers compatible with their intumescent paints. (If you are purchasing paint through us we will give a detailed specification of what primer and intumescent will be compatible for the job) Check product datasheets for specific recommendations.
- Application: Apply the primer evenly using a brush, roller, or airless sprayer, depending on the steel structure’s size and complexity. Ensure you achieve the specified dry film thickness (DFT) outlined by the manufacturer.
- Drying Time: Allow the primer to cure completely before proceeding. Factors like temperature and humidity will influence drying times.
Step 3: Applying Intumescent Paint
Once the primer has cured, the intumescent paint can be applied. This step is where the fire-protective qualities are built into the coating system.
- Product Selection: Choose a trusted brand, such as Nullifire SC801, Jotun SteelMaster, or Thermoguard Thermocoat, based on the fire protection requirements and project specifications. Each brand provides unique solutions for different durations of fire resistance (30, 60, 90 or 120 minutes) We can help find the best paint for the best price for your job contact us with your enquiry.
- Mixing: Before application, thoroughly mix the paint according to the manufacturer’s instructions. Mechanical stirrers are often recommended for consistency.
- Application Techniques:
- Brushing: Suitable for smaller areas or touch-ups. Use a high-quality brush for even coverage, but note that brushing may require additional coats to achieve the required DFT.
- Spraying: For larger surfaces, airless spraying is faster and delivers a more uniform finish. Adjust the spray settings based on the product’s viscosity and the desired film thickness.
- Coat Thickness: Achieving the specified DFT is critical for fire protection. Use a wet film gauge during application to monitor thickness and ensure compliance with the manufacturer’s guidelines. (view our DFT gauge) – (We also have a video on how to take measurement of intumescent paint.)
- Curing: Allow each coat to dry as per the product’s datasheet. Environmental conditions, such as temperature and humidity, can impact curing times.
Step 4: Applying a Top Coat
A topcoat is optional but highly recommended for intumescent paint systems exposed to harsh environments, such as outdoor structures or high-traffic areas.
If you are unsure whether you need a top coat you can contact us.
- Purpose: Topcoats protect the intumescent layer from moisture, UV radiation, and physical wear.
- Choosing a Topcoat: Brands like Envirograf and Jotun offer topcoats that complement their intumescent systems. Select a topcoat with the desired finish (e.g., matte or gloss) and durability.
- Application: Apply the topcoat using similar methods as the intumescent paint. Ensure it is compatible with the intumescent layer to avoid chemical reactions or peeling.
- Maintenance: Regular inspections will help identify wear or damage to the topcoat, which should be repaired promptly to preserve the system’s integrity.
Best Practices and Tips
- Always consult the product datasheets for specific application instructions and compatibility information. At International Passive Fire we can provide detailed technical support to ensure correct usage.
- Monitor environmental conditions, such as temperature and humidity, during application. Extreme conditions can affect curing and performance.
- Perform regular quality checks throughout the application process, such as adhesion tests and thickness measurements.
- For complex projects or large structures, consider hiring certified applicators to ensure compliance with safety standards and manufacturer warranties.
By following these steps, you’ll achieve a durable, effective fire protection system for your steel structure. Whether using Nullifire’s advanced SC products, Jotun’s SteelMaster series, or Sherwin-Williams’ Firetex coatings, adhering to proper application practices will maximize the performance and lifespan of your intumescent paint system.